Planetary Gearbox Design and Development using Additive Manufacturing
Authors:
Article info
2023-08-31
2023-10-30
2024-01-27
48 - 53
Keywords
- System
- Assembly;
- manufacturing;
- Planetary
- 3D
- printing;
- Additive
- gearbox
Abstract
Modern manufacturing technology is dominated by additive manufacturing due to its simplicity, precision, time and material savings, and flexibility in design. The purpose of this study is to propose and print a 3D model of planetary gear trains since these gear trains are more efficient than conventional gear trains and have many advantages. A planet gear trains must have collinear input and output axes in order to achieve compact space requirements. Using even spacing between the planets in a gear train allows both static and dynamic forces to be balanced. It is also possible for multiple planets to produce high torques. Finally, it is capable of providing a wide range of speeds. The printed model performed exceptionally well when it came to performance, and it can be used for both educational and industrial purposes, exhibiting the ability to withstand a high level of stress. The current paper demonstrated the process of 3D printing and the challenges involved in printing planetary gear trains, as well as possible solutions to these challenges. Finally, tolerances were reported as 0.5 mm on the final CAD model, and 0.15 mm on the last updated results.
Amer, M., Lin, C.-C., Ismail, H., Wu, S.-H., Lu, B.-R., Wu, Z.-Y., Chen, S.-F., & Cheng, C.-W. (2024). Planetary Gearbox Design and Development using Additive Manufacturing. An-Najah University Journal for Research - A (Natural Sciences), 38(1), 48–53. https://doi.org/10.35552/anujr.a.38.1.2150
[1]M. Amer et al., “Planetary Gearbox Design and Development using Additive Manufacturing,” An-Najah University Journal for Research - A (Natural Sciences), vol. 38, no. 1, pp. 48–53, Jan. 2024, doi: 10.35552/anujr.a.38.1.2150.
Amer, Mohammed, et al. “Planetary Gearbox Design and Development Using Additive Manufacturing.” An-Najah University Journal for Research - A (Natural Sciences), vol. 38, no. 1, Jan. 2024, pp. 48–53. Crossref, https://doi.org/10.35552/anujr.a.38.1.2150.
1.Amer M, Lin CC, Ismail H, Wu SH, Lu BR, Wu ZY, et al. Planetary Gearbox Design and Development using Additive Manufacturing. An-Najah University Journal for Research - A (Natural Sciences) [Internet]. 2024 Jan;38(1):48–53. Available from: http://dx.doi.org/10.35552/anujr.a.38.1.2150
Amer, Mohammed, Chung-Cheng Lin, Hasan Ismail, Shin-Hung Wu, Bo-Rong Lu, Zhang-Yang Wu, Shih-Feng Chen, and Chung-Wei Cheng. “Planetary Gearbox Design and Development Using Additive Manufacturing.” An-Najah University Journal for Research - A (Natural Sciences) 38, no. 1 (January 2024): 48–53. https://doi.org/10.35552/anujr.a.38.1.2150.
Planetary Gearbox Design and Development using Additive Manufacturing
المؤلفون:
معلومات المقال
2023-08-31
2023-10-30
2024-01-27
48 - 53
الكلمات الإفتتاحية
- System
- Assembly;
- manufacturing;
- Planetary
- 3D
- printing;
- Additive
- gearbox
الملخص
Modern manufacturing technology is dominated by additive manufacturing due to its simplicity, precision, time and material savings, and flexibility in design. The purpose of this study is to propose and print a 3D model of planetary gear trains since these gear trains are more efficient than conventional gear trains and have many advantages. A planet gear trains must have collinear input and output axes in order to achieve compact space requirements. Using even spacing between the planets in a gear train allows both static and dynamic forces to be balanced. It is also possible for multiple planets to produce high torques. Finally, it is capable of providing a wide range of speeds. The printed model performed exceptionally well when it came to performance, and it can be used for both educational and industrial purposes, exhibiting the ability to withstand a high level of stress. The current paper demonstrated the process of 3D printing and the challenges involved in printing planetary gear trains, as well as possible solutions to these challenges. Finally, tolerances were reported as 0.5 mm on the final CAD model, and 0.15 mm on the last updated results.
Amer, M., Lin, C.-C., Ismail, H., Wu, S.-H., Lu, B.-R., Wu, Z.-Y., Chen, S.-F., & Cheng, C.-W. (2024). Planetary Gearbox Design and Development using Additive Manufacturing. An-Najah University Journal for Research - A (Natural Sciences), 38(1), 48–53. https://doi.org/10.35552/anujr.a.38.1.2150
[1]M. Amer et al., “Planetary Gearbox Design and Development using Additive Manufacturing,” An-Najah University Journal for Research - A (Natural Sciences), vol. 38, no. 1, pp. 48–53, Jan. 2024, doi: 10.35552/anujr.a.38.1.2150.
Amer, Mohammed, et al. “Planetary Gearbox Design and Development Using Additive Manufacturing.” An-Najah University Journal for Research - A (Natural Sciences), vol. 38, no. 1, Jan. 2024, pp. 48–53. Crossref, https://doi.org/10.35552/anujr.a.38.1.2150.
1.Amer M, Lin CC, Ismail H, Wu SH, Lu BR, Wu ZY, et al. Planetary Gearbox Design and Development using Additive Manufacturing. An-Najah University Journal for Research - A (Natural Sciences) [Internet]. 2024 Jan;38(1):48–53. Available from: http://dx.doi.org/10.35552/anujr.a.38.1.2150
Amer, Mohammed, Chung-Cheng Lin, Hasan Ismail, Shin-Hung Wu, Bo-Rong Lu, Zhang-Yang Wu, Shih-Feng Chen, and Chung-Wei Cheng. “Planetary Gearbox Design and Development Using Additive Manufacturing.” An-Najah University Journal for Research - A (Natural Sciences) 38, no. 1 (January 2024): 48–53. https://doi.org/10.35552/anujr.a.38.1.2150.
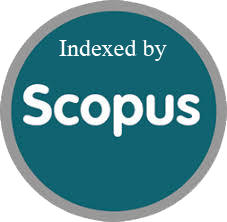
Since 2019
Cite Score (Scopus): 0.8
Time to First Decision: 5 Days
Submission to Acceptance: 90 Days
Acceptance to Publication: 14 Days
Acceptance Rate: 22%
Call for Papers:
Sustainable Materials and Chemistry for Energy and Environmental Applications
Why should you
Publish With Us?
An-Najah National University
Nablus, Palestine
Nablus, Palestine
- P.O. Box
- 7, 707
- Fax
- (970)(9)2345982
- Tel.
- (970)(9)2345560
- (970)(9)2345113/5/6/7-Ext. 2628
- [email protected]
- EIC
- Prof. Waleed Sweileh
An-Najah University Journal for Research - A (Natural Sciences) by An-Najah University, Nablus, Palestine is licensed under CC BY-NC 4.0